A total of about 1,600 kg/ton-hot
metal of such iron-bearing materials as sintered ore, lump ore
and pellets, and about 380 kg/ton-hot metal of coke as the reductant
are charged in alternate layers from the top of the BF. It has
recently become common practice to inject usually 90-120 kg/ton-hot
metal of pulverized coal as part of the reductant from the tuyeres
in the lower part of the furnace. At present, heavy-oil injection
from the tuyeres is rarely used for economic reasons. Approximately
1,000 Nm3/ton-hot metal of hot blast is also blown through the tuyeres after preheating to 1,423-1,523K (1,150-1,250 ) at the hot
stoves. The humidity and oxygen concentration of the hot blast
are also controlled.
The hot blast reacts with the coke and pulverized coal in the
belly and bosh of the BF to form a mixture of carbon monoxide
and nitrogen. This mixture ascends in the furnace while exchanging
heat and reacting with the raw materials descending from the
furnace top. The gas is eventually discharged from the furnace
top and recovered for use as fuel in the works. During this process,
the layer-thickness ratio of iron-bearing materials to coke charged
from the furnace top and their radial distribution are controlled
so that the hot blast can pass with appropriate radial distribution.
During the descent of the burden in the furnace, the iron-bearing
materials are indirectly reduced by carbon monoxide gas in the
low-temperature zone of the upper furnace. In the lower part
of the furnace, carbon dioxide, produced by the reduction of
the remaining iron ore by carbon monoxide is instantaneously
reduced by coke (C) into carbon monoxide which again reduces
the iron oxide. The overall sequence can be regarded as direct
reduction of iron ore by solid carbon in the high-temperature
zone of the lower furnace. The reduced iron simultaneously melts,
drips, and collects as hot metal at the hearth. The hot metal
and molten slag are then discharged at fixed intervals (usually
2-5 hours) by opening the tapholes and cinder notches in the
furnace wall.
The materials discharged from the BF are hot metal at 1,803K
(1,530 ), about 300 kg/ton-hot metal of molten
slag, and dust-bearing exhaust gas discharged from the furnace
top. Hot metal is poured into a torpedo car, where it is subjected
to hot metal pretreatment, and then transferred to the steelmaking
plant. Molten slag is crushed after cooling and is recycled as
a material for roadbed and cement. After dust removal, the exhaust
gas is used as a fuel for the reheating furnaces.
The capacity of a BF is expressed by the weight of hot metal
that can be produced per day. Representative technical indicators
stand for (i) the tapping ratio, which shows the tapped quantity
of hot metal per day per m3
of inner volume of the furnace, and(ii) the fuel ratio, which
shows the consumption of coke andauxiliary fuel required per ton of hot metal. In Japanese BFs,tapping ratios of 1.7-2.1 ton/m3/day
and fuel ratios of 470-500 kg/ton are typical.
The greatest tasks to be achieved in blast-furnace operation
are to decrease the unit energy consumption, ensure stable operation
in terms of the tapped quantity, composition, and temperature,
and to extend the life of the furnace. In recent large-scale
BFs, unit energy consumption has been decreased to 13 gigajoules/ton-hot
metal, out of which the energy required for ore reduction accounts
for about 60%.
Careful preparation of raw materials for physical and chemical
consistency is an effective way of stabilizing operation over
long periods. It is also necessary to understand the physical
and chemical behavior accurately in each part of the furnace
during operation. For this purpose, monitoring the conditions
inside the furnace and applying artificial intelligence for data
processing and judgment have been put into practical use with
great success. For the future, it will be necessary to understand
the complex conditions inside the furnace and use such data to
further stabilize furnace operations.
Because blast-furnace relining is extremely expensive, total
production costs can be reduced substantially by extending furnace
life. Technological advances in operation and maintenance to
date have extended the life of BFs to as long as 16 years (current
record), but further technical development is desired to extend
furnace life to twenty years or more. |
|
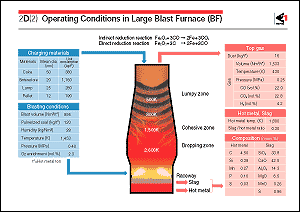 |
 |
 |
|
|