The blast furnace (BF) has a vertical
cylindrical structure externally covered with a shell of thick
steel plate and internally lined with refractories. The refractory
structure is cooled by water-cooled metal components called staves,
which are embedded between the shell and the refractories. The
furnace body is composed of (i) the shaft, which tapers outward
from the top, (ii) the belly, which is a straight cylinder, (iii)
the bosh, which tapers inward toward its bottom and is located
immediately under the belly, and (iv) the hearth, at the bottom
of the furnace. The shaft, belly, and bosh are usually lined
with chamotte brick and silicon-carbide brick, and the hearth
is lined with carbon brick. Depending on the size of the furnace,
the side wall of the hearth is radially fitted with some 20 to
40 of water-cooled copper tuyeres, which are used to inject the
hot blast into the furnace from the hot stoves through the hot-blast
main and bustle pipes. Tapholes for discharging hot metal and
cinder notches for discharging slag are also installed in the
hearth section. The largest BFs at present are about 80m in
total height, with a furnace body height of about 35m and a maximum
internal diameter of about 16m, and have an internal volume of
about 5,200m3. A furnace of this size can produce approximately
10,000 tons of hot metal a day.
All BFs have auxiliary equipment such as (i) belt conveyors for
transporting raw materials (ore and coke) to the furnace top,
(ii) hoppers for temporarily storing these raw materials, (iii)
a bell-type or bell-less-type device for charging the raw materials
into the furnace with appropriate distribution in the radial
direction, (iv) hot stoves for heating the blast, (v) blowers
for feeding the blast, and (vi) equipment for dust removal, and
recovering and storing the gas from the furnace top. Blast furnaces
in which pulverized coal is injected from the tuyeres (PCI =
pulverized-coal injection) are provided with equipment for pulverizing
the coal and feeding it under pressure. With bell-type charging
equipment, the raw materials enter the furnace through the gap
created by moving down a small inverted bell. This bell closes
and a larger bell (big-end-down) opens to allow material to fall
into the shaft below. With bell-less charging equipment, the
raw materials are dropped into the furnace through a rotating
chute. The hot stove is a cylindrical furnace about 12m in diameter
and some 55m in height, and has a chamber filled with checkered
silica bricks. The hot stove is a type of heat exchanger in
which the heat produced by combustion of the BF gas is stored
in the checker-work chamber, after which cold air is blown through
the hot checker-work to produce the preheated hot air blast to
the furnace. Two or more stoves are operated on alternate cycles,
providing a continuous source of hot blast to the furnace.
A BF is usually operated with a furnace-top pressure of about
250 kilopascals. To recover the energy from the large volume
of high-pressure exhaust gas, the BF is equipped, after dust
removal, with a top-pressure recovery turbine (TRT), for generating
electric power by utilizing the pressure difference between the
furnace-top and gas storing holder. |
|
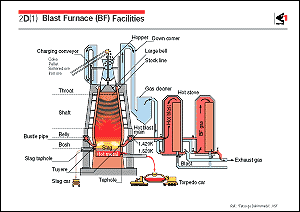 |
 |
 |
|
|