Increasingly stringent quality
requirements have heightened the demand for steels with very
low levels of impurities such as phosphorus, sulfur, hydrogen,
nitrogen, and oxygen, and of nonmetallic inclusions such as MnS,
SiO2, and Al2O3. Such high purity cannot be attained by BOF blowing
for decarburization since its refining capability is limited.
Hot metal produced in the BF is conventionally transferred either
to a ladle or to a vessel called a torpedo car and is then charged
into the BOF. The oxygen blowing process in which hot metal is
decarburized and converted to steel is carried out mostly in
the BOF. However, a method for dividing the refining capability
and allocating the divided function to processes before and after
the BOF has been put into practical use.
The processes in which impurities are removed from the hot metal
are called hot metal pretreatment, whereas the processes in which
the molten steel tapped from the BOF is subjected to further
refining and degassing are called secondary refining. At present,
an integrated process of smelting in the BF, hot metal pretreatment,
decarburizing in the BOF, and secondary refining has become the
standard manufacturing process for high grade steels.
Hot metal pretreatment includes the desiliconization, dephosphorization,
and desulfurization of hot metal. The silicon in the hot metal
is oxidized in the BOF, where it reacts with added lime (CaO)
and iron oxide (FeO) to form a CaO-FeO-SiO2 slag. If the silicon
content of the hot metal is low, this reaction is shortened in
the BOF, the production efficiency is improved, and the volume
of slag generated is small; therefore, decarburizing with a high
iron yield is possible. Desiliconization is therefore conducted
as a pretreatment process by adding iron oxides such as mill
scale and sintered ore fines to hot metal in the runners in the
casthouse of the BF or in the transfer vessel.
Dephosphorization is usually carried out by injecting a dephosphorizing
agent containing lime, iron oxide, fluorspar, etc. into the hot
metal in the transfer ladle or torpedo car together with a gas.
This promotes the transfer of the phosphorus in the hot metal
to the slag phase, which is then discharged. Dephosphorization
is usually carried out after desiliconization, because the dephosphorization
reaction proceeds more quickly at lower silicon contents. Although
hot metal is desulfurized to some extent by the dephosphorization
treatment, extra low sulfur steels require further desulfurization,
which is performed by separate injection of desulfurizing agents
such as CaO, Na2CO3, CaC2, and Mg into the hot metal.
Such treatments can be made more effective by identifying and
enhancing the elementary rate steps that control the dephosphorization
and desulfurization processes. A good understanding of thermodynamics
and transport phenomena is indispensable in achieving these objectives. |
|
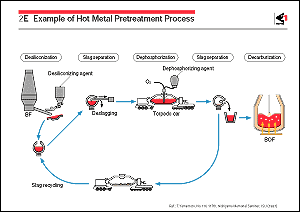 |
 |
 |
|
|