In the smelting process for iron
and steel, coke serves as the source of carbon, which works as
a reducing agent when reducing iron ore in the BF. At the same
time, coke acts as the heat source for heating and melting the
charged materials. Coke is made by baking coal in a coke oven.
Coal is classified into the four grades shown in the figure,
anthracite being the highest grade. Typical types are bituminous
coal and brown coal. Bituminous coal exists in the largest quantities,
having estimated reserves worldwide of approximately 7 trillion
(trillion=1012)tons, with
confirmed reserves of approximately 2 trillion tons.
The coke used in the BF must have a high carbon content and low
ash and sulfur contents, and must have an appropriate porosity
as well as good strength to ensure that it gives good reactivity
and does not pulverize to choke the gas flow in the BF even at
high temperatures. Cokes that meet these requirements are derived
from bituminous coals that combine good coking properties with
low ash and sulfur contents.
In the coke oven, the raw coal obtained by crushing and blending
is charged into the coke chamber, where it is then baked (carbonized)
by indirect heating at 1,473-1,573K (1,200-1,300 ) for 14-18
hours to form coke that contains about 90% fixed carbon. The
coking process also produces such by-products as gas, coal tar,
and pitch which can be refined and treated into useful secondary
products such as fuel gas, pure hydrogen gas, chemical products
such as benzene, toluene, xylene, naphthalene, dye, and carbon
fibers.
The life of a coke oven is about 40 years. In Japan, the lives
of the coke ovens now in operation will begin to expire successively
about the year 2015, which is expected to result in a shortage
of coke. However, to cope with this problem, pulverized coal
injection, in which coal with a poor coking property is injected
through the tuyeres into the BF, is widely used. In addition,
technical developments are being made to provide new technology
to (i) produce coke or (ii) establish a cokeless iron making
process, both of which will make it possible to select raw coal
materials more freely and will cause less environmental pollution. |
|
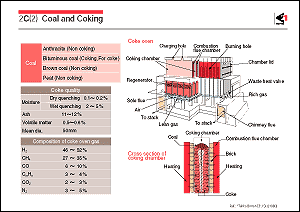 |
 |
 |
|
|