Among the elements composing the
crust of the earth, iron exists in the largest quantity next
to oxygen, silicon, and aluminum. Iron exists as natural ores
in the form of oxides, and the estimated amount of ore deposits
in the world is approximately 800 billion tons. Typical ores
are hematite (Fe2O3)
and magnetite (Fe3O4),
having theoretical iron contents of 70% and 72%, respectively.
The iron content of practical ores is about 65% at maximum, and
these ores include 2-6% silica and 1-3% alumina (Al2O3).
Representative sources of iron ores are found in mainland China,
Brazil, Australia, the former USSR, America, India, Canada, South
Africa, and elsewhere. The phosphorus and sulfur contents of
ores differ greatly according to their origin.
High-grade iron ore is crushed for sizing, producing both fine
ore as well as lump ore. To beneficiate low-grade ore, it is
first pulverized into finer particles called pulverized ore.
Both fine and pulverized ores are then subjected to pre-treatments
before they are charged into the BF; that is, the fine ore is
processed into sintered ore by sintering, and pulverized ore
is processed into pellets by pelletizing. In Japan, the proportions
of iron ores charged into the BF are, at present, 15% lump ore,
10% pellets, and 75% sintered ore. Thus, pretreated iron ores
represent a large majority of the ore used.
In the sintering process, fine ores 2-3mm in diameter are mixed
with coke breeze as a fuel. Burnt limestone powder is used as
a flux. These materials are charged in an iron box called a pallet
before being ignited. Fine ore particles are partially melted
and combined by the combustion heat of the coke to form an agglomerate
which is then subjected to crushing and screening processes in
order to obtain sintered ore 15-30mm in diameter. The Dwight-Lloyd
type of sintering machine is mainly used, sintering being conducted
continuously by transferring pallets placed on a caterpillar.
Pelletizing is a process that involves mixing very finely ground
particles of ore of less than 200 mesh with fluxing materials
such as limestone and dolomite and then shaping them into balls
10-15mm in diameter by a pelletizer, and hardening the balls
by firing with heavy oil and/or coal as a fuel. Cold-bond pellets
are also produced by pelletizing, and do not require firing.
At present, small-scale equipment for producing cold-bond pellets
is in operation mainly to treat the dust collected in steel works.
This technology offers great promise for the future in terms
of energy-saving and reducing environmental pollution.
Compared with sintered ore, pellets have a higher iron- and a
lower gang-content, and pelletizing is suitable for treating
the very fine ore that will predominate in the future. However,
pellets have the disadvantages that more fossil fuel is consumed
during pelletizing and it is difficult to control the radial
distribution of the thickness of pellets charged in the BF. |
|
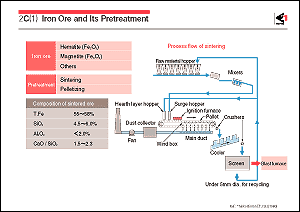 |
 |
 |
|
|