Figure(a) shows that an increase
in stirring power density applied to the steel bath
intensifies circulation of the molten steel and reduces the uniform
mixing time . Regardless of the stirring method
employed, the relationship shown in this figure holds true, and
the time required for uniform mixing can be reduced by as much
as one order of magnitude if molten steel is stirred at 200 W/ton.
How much the overall mass transfer rate increases with increased
stirring of the steel bath and an increased circulating flow
rate is shown next by several examples. Figure(b) shows a case
in which the uniform mixing time was significantly
reduced by blowing gas into the steel bath from the furnace bottom
of the BOF. When is short and the circulating flow
rate Q of the molten steel is high, the mass flux of carbon transferred
to the zone where oxygen gas comes into contact with the steel
bath also becomes large. Therefore, the mass transfer rate of
carbon increases, carbon is preferentially oxidized and decarburized,
and the degree of oxidization of molten steel due to the formation
of iron oxide and of iron loss in the slag becomes low. This
advantage is especially great when the target carbon content
becomes low, as shown in Fig.(c). The index used in this figure
is the value obtained by dividing the product of partial pressure
Po2 of oxygen in the furnace and oxygen
volume Vo2 supplied per unit time to the reaction interface (mass flux of oxygen) by the product of circulating flow rate Q of the molten steel and specific weight r of the molten steel (corresponding to the mass flux of carbon). This index is called the ISCO value (index for selective carbon oxidation).
The value in a top-blown BOF is a little more
than 100 seconds in Fig.(b), while the ISCO value corresponding
to this value is about 230 in Fig.(c). The value
in bottom-blown BOF is about 12 seconds, and the
corresponding ISCO value is about 60. As shown in Fig.(c), with
decreasing from a little more than 100 seconds to
12 seconds and the corresponding ISCO value decreasing from 230
to 60, the iron oxide in slag that is formed by oxidation of
steel decreases substantially from about 23% to 10% as the total
iron content. As a result of stirring, shorter (higher Q), that
is, a lower ISCO value, will result in a higher overall mass
transfer rate of carbon for the oxidation, and hence smaller
oxidation loss of molten steel, giving higher iron yield.
The relationship that the overall mass transfer increases substantially
with increasing Q or 1/ holds true not only for
the decarburization that occurs between gas and metal, but also
for the dephosphorization and desulfurization that occur between
slag and metal. Furthermore, this relationship also holds true
for the deoxidation that removes oxide inclusions such as alumina
formed and suspended in the steel bath after adding a suitable
deoxidizing agent such as aluminum. The result of bottom-blowing
argon gas into the aluminum-killed stainless steel bath in a
vacuum oxygen decarburization (denoted VOD hereinafter) furnace
is shown in Fig.(d) as an example of this. When the bottom-blown
gas flow rate was increased from 20 to 70 N /min, Q increased
from 10 to 40 ton/min and, as a result, the mass transfer coefficient
for alumina inclusion removal (deoxidation) was doubled from
1 to 2/min. Vortices are generated by stirring molten steel,
and due to the velocity gradient in the vortices, inclusions
collide with each other, coalesce, and become large. When their
critical diameter is exceeded, these inclusions float outside
of the system. Higher Q and higher result in a
higher value of k, because the number of vortices and the velocity
gradient in the vortices both increase.
These various blowing and stirring operations are used for smelting
and refining reactions and, as a result, remarkable progress
has been achieved in the iron and steelmaking processes. This
procedure has been developed to the extent that a region of high
oxygen potential and low temperature is intentionally formed
in one part of a reactor, a region of low oxygen potential and
high temperature is intentionally formed in another part, and
dephosphorization and desulfurization are simultaneously promoted
in the former and latter regions, respectively. This technique
has been put into practical use as a simultaneous dephosphorization
and desulfurization process for pretreating hot metal and has
substantially reduced the dephosphorization and desulfurization
load in BOF blowing. |
|
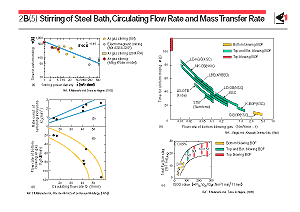 |
 |
 |
|
|