New ironmaking processes have been
extensively explored with a view to saving resources and energy,
as well as reducing environmental pollution.
The figure shows the Corex process developed in Austria. This
process is the only new ironmaking process now commercialized,
and is in operation with plants having capacities of up to 600,000
ton/year.
In the Corex process, a combination of lump ore, pellets, and
sinter is pre-reduced to about 90% metallization (sponge iron)
in the reduction shaft furnace by a gas containing CO and H2
supplied from the melter gasifier, which is the main reactor
of the Corex plant. The sponge iron is delivered as hot from
the reduction shaft furnace by screw conveyors into the melter
gasifier where melting takes place. Non-coking coal lump less
than 50mm and larger than 6mm in diameter is also fed into the
reactor. When the coal comes into contact with the hot gas, the
coal is dehydrated and degasified and forms a coke bed. In the
lower part of the coke bed, the coke generated is gasified in
an exothermic reaction which results in temperatures of more
than 2,700K. The hot gas, which mainly consists of carbon monoxide,
flows from the fluidized bed to the top of the reactor. Slag
and hot metal layers are maintained in the bottom of the reactor.
The upper part of the reactor is designed as freeboard.
The raw gas from the reactor has a temperature of about 1400K
in the freeboard. In the hot dust cyclones, the gas is cleaned
of the major part of the entrained coke dust, and is used to
reduce the iron sources charged in the reduction shaft furnace.
Other new processes for iron making have been attempted in Australia
(HIsmelt- and Ausmelt- process), Japan (DIOS process), Russia
(Romelt process), and U.S.A. (AISI process), but are still at
the pilot plant stage. These processes utilize mainly smelting
reduction, meaning that the amount of reduction in the molten
state is greater than that in the solid state, which is different
from that in the BF process. These processes should offer advantages
such as; (i) iron ore can be used without agglomeration; (ii)
non/weak-coking coals can be used directly without coking; (iii)
start up and shut down in operation are much easier than with
a BF, and (iv) less carbon dioxide is produced. However, many
problems have yet to be solved before these processes will become
a commercial reality, requiring much research and development. |
|
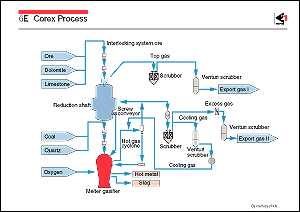 |
 |
 |
|
|