One feature of steel materials
is their recyclability. Steel used in civil engineering, construction,
shipbuilding, automobiles, home electrical appliances, containers,
etc. is recovered as steel scrap. In any country, increasing
per capita stock of steel ( ca.10 ton/head)
usually increase the generation and recycling of waste steel
scrap, although the local availability of hot metal and electricity
causes some differences. A general trend during the past decades
is that scrap-based steelmaking has increased its share, reaching
around 49% of global crude steel production in 1994. The recycling
of iron and steel scrap to steel melting shops is schematically
described in the figure. In 1993, 456 million tons of scrap was
generated worldwide, comprising obsolete scrap (272million tons),
home scrap (88million tons), and prompt industrial scrap (96million
tons). However, with the development of steel materials for higher
grades and higher performance, use of steel materials in combination
with nonferrous metals or nonmetallic materials has increased.
It is estimated that non-volatile residuals (tramp elements)
such as Cu, Sn, As, Sb, and Bi, especially Cu and Sn included
in obsolete scrap will accumulate in the recycling of scrap by
about 30% in 20 years if the present situation continues.
The use of coated steels has increased during the last decade,
mainly due to the galvanizing of sheets for the auto industry.
In 1994, the amount of metal-coated steels produced within the
European Union and Japan was, respectively, 19.5 and 16.0 million
tons of which tin plate corresponded to 4.0 and 2.0 million tons,
electro-chromium coated steels 0.7 and 2.0 million tons, and
other metal coated steels 14.8 and 12.0 million tons, mainly
galvanized. Organic materials in the coating generate harmful
dioxines, and volatile residuals such as Zn and Pb cause metal
and/or metal oxide fumes which are hazardous.
In recycling, home scrap and prompt industrial scrap do not present
major problems since their chemistry is well known and quality
acceptable. The problem is obsolete scrap, which is estimated
to account for about 2.7% (37million tons) of the accumulated
total stock of steel (1,300million tons) in the year 2000 in
Japan. This means that the percentage of obsolete scrap to total
annual production of crude steel (e.g. 100million tons) becomes
a high 37%.
Recycling of steel scrap considerably contributes to the reduction
of energy consumption and CO2 evolution
as discussed in the next section which follows, except for the
residuals constraint.
For residuals, there seems to be only a few commercial means
of mechanically removing mixed residuals by an enhanced shredding
process or coated residuals by electrolytic leaching or vacuum
heating. Virtually no economically feasible means have been developed
as yet to remove the residuals alloyed in steel. Numerous trials
have been made, but the methods tested have been inadequate to
overcome the cost barrier. The current status of the processes
for residuals removal is technically in progress, but not competitive
at the commercial level.
Many problems remain unresolved for promoting further recycling
of iron resources to maintain the quality of steel products in
the future while preventing quality fluctuation of the steel
scrap. It is expected that these problems will be resolved with
future steelmaking processes. |
|
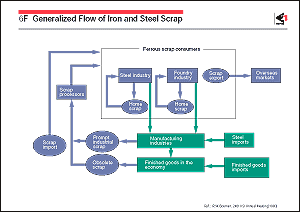 |
 |
 |
|
|