About 500 kg of coke is consumed
to produce one ton of hot metal. As mentioned earlier, coke plays
a necessary role in the BF ironmaking process in the chemical
reaction. However, maintaining good permeability of gases is
also an important role of coke in the conventional BF process.
Good quality coke is indispensable to the BF-BOF process route,
and hence coke ovens comprise an important part of the integrated
steel mill.
The construction of Japan's integrated steel mills was completed
in the 1970s. Most Japanese coke ovens will reach the end of
their service lives in the early 21st century, after about 40
years of operation, which is the expected life of coke ovens.
The case for North American and European mills is similar.
Since the BF cannot be operated without coke, efforts have been
made to prolong coke oven life and to decrease coke consumption.
Significant improvement can be seen in repair technologies for
coke oven refractories, pulverized coal injection into the BF,
and development of the formed coke process, supported by a national
fund during 1978 - 1986 in Japan.
However, pulverized coal injection and the formed coke process
cannot replace all the coke consumed in the BF. New production
capacity will soon be needed to replace aging coke ovens. The
present coke-making process has drawbacks such as emissions of
particulates and harmful gases, low productivity, entailing high
equipment cost, and high energy consumption due to high temperature
processing, which discourage the construction of new capacity.
After two years of conceptual and fundamental studies, The Japan
Iron and Steel Federation (JISF), sponsored by the government,
began the development of a new coke-making process in 1996. The
project is called SCOPE 21, or Super Coke Oven for Productivity
and Environment for the 21st Century, and consists of three years
of bench-scale tests followed by three years of pilot plant tests.
The concept of the new coke-making process, as shown in the figure,
consists of three sub- processes of coal pretreatment and coking,
followed by heat treatment and quenching:
(i) The coking properties of coal are improved in the pretreatment
process, where coal particles are rapidly heated to 573-673K
(300-400 ).
(ii) In the coking process, the pretreated coal is agglomerated and heated to approximately 1,000K (727 ). This temperature
is substantially lower than in the conventional coke oven, where
the temperature rises to 1,273K (1,000 ). Uniform heating
of the agglomerate makes low temperature coking possible.
(iii) The coke thus produced undergoes heat treatment and quenching,
in which the coke is stabilized to obtain necessary quality for
the BF.
In comparison with conventional coke ovens, the project aims
at: increasing the use of non-coking coal from 20% to 50%, virtual
elimination of particle and fume emissions and a 30% reduction
of NOx, fully automated unmanned operation, energy conservation
by 20%, and improved productivity by 300%. |
|
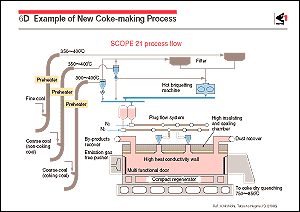 |
 |
 |
|
|