Heating and melting furnaces, smelting
and refining furnaces, and the vessels used to carry hot metal
and molten steel are all lined with refractories. The main reason
why these furnaces and vessels cannot be used continuously is
the need for repair and replacement as a result of wear of the
refractory lining. In other words, the life of the refractories
determines the life of furnaces and vessels. Refractories for
iron and steel production are used under very severe conditions,
which include not only elevated temperatures, but also thermal
shock caused by abrupt temperature changes. Further, they must
possess high-temperature strength and wear resistance to the
large momentum of impinging and turbulent metal flow. Refractories
must also have the chemical stability to withstand attack by
hot metal, molten steel, slag, and various fluxes.
Refractories have a high melting point and good heat-insulating
properties. Their basic composition comprises chemically stable
substances such as magnesia, alumina, and silica which do not
easily react with steel slags or fluxes. When binders are mixed
with these refractories, the mixture, when used as it is, is
called a monolithic refractory; when pressurized, compacted,
and fired, it is called firebrick.
The figure shows the progress in the unit consumption of refractories
(weight of refractories consumed to produce one ton of crude
steel) in Japan. Unit consumption decreased by as much as 60%
from 1970 onwards for two main reasons: (i) changes in blowing
and casting processes, which are typified by the change from
the open hearth furnace to the BOF, and the replacement of ingot
casting by the continuous casting process; and (ii) the extension
of the life of refractories by improvement in their quality as
well as progress in application techniques.
An example of quality improvement of the furnace-bottom carbon
brick in the BF is a decrease in the penetration of slag and
iron achieved by adding silicon and a reduction in wear damage,
by adding alumina. These measures have contributed greatly to
extending the furnace life. At present, the BOF and EAF are
lined mainly with fired magnesia-carbon brick which is a composite
material that maintains the high corrosion resistance to basic
slag and molten metal of magnesia, while enhancing thermal shock
resistance, which was the weak point of magnesia brick, by adding
carbon. Porosity is reduced by firing this brick at high temperatures
in reducing atmosphere to prevent penetration by slag and molten
steel. In the BOF, progress in related techniques, together
with the above-mentioned improvements in quality, has also contributed
to the extension of the life of refractories. Typical examples
are, (i) zone lining, in which a brick of optimum composition
is used for each zone of the furnace; (ii) slag-coating of the
inner walls of the vessel; and (iii) decreasing thermal shock
to the refractories by eliminating tilting of the vessel for
reblowing, which has become possible due to the improved hit
ratio achieved through improved BOF operation.
At the continuous caster, the ladle and tundish are lined with
a powdery monolithic refractory material which is applied by
stamping or gunning. The consumption of monolithic refractories
has been increasing because mechanization and automatization
have made production and application easier, and since 1988,
the use of monolithic materials has exceeded that of firebrick.
Repeated use of ladles and tundishes while still hot from previous
use has also extended their service life substantially because
the thermal stress arising from cooling and reheating is minimized
and hence resulting spalling of the refractories can be avoided.
This repeated "as-hot" use has been made possible
by the development of robotized automation of repair and maintenance
of hot tundishes in combination with advanced hot gunning of
refractories to points where damage is observed.
Submerged entry nozzles used to deliver molten steel from the
tundish into the mold are made of alumina-graphite refractories
of higher corrosion resistance, which have replaced fused-silica
refractories. Carefully thought-out refractory development for
other equipment has also resulted in higher-quality refractories
suitable for specific service environments. |
|
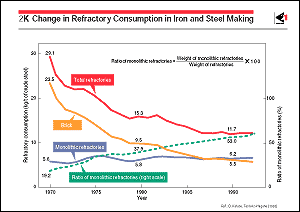 |
 |
 |
|
|