The productivity and yield that
are so important for operating a continuous caster can be markedly
improved by casting many heats continuously without interrupting
casting. This is called continuous-continuous casting or sequence
casting, and has the advantage of eliminating the need for preparations
for starting casting. Consequently, productivity is increased
and the amount of the cast strand which must be cropped at the
initial and final casting positions due to poor quality is decreased.
Techniques have been developed for sequence casting, which allow
the mold width to be changed and different steel grades to be
cast without interrupting casting operations. These allow strands
of different width and grade to be cast continuously without
interruption. Submerged entry nozzles wear and become clogged
as throughput of the melt increases; therefore, methods have
been developed for the quick, automatic exchange of submerged
entry nozzles without suspending the casting operation. As one
extremely serious practical problem, in "breakout",
the solidified shell grows unevenly, the thinner portion of the
shell ruptures, and the molten steel leaks from the mold, requiring
a full stop of the line. Thermal monitoring techniques for predicting
breakout are used at many casters. Productivity can be improved
by raising the casting speed, as well as by improving the operating
rate. Progress in techniques and equipment has now enabled a
casting speed of 1.5-2.8 m/min in continuous slab casters, which
corresponds to a production capacity of 5 ton/min per strand.
Thus, approximately 3.6 million ton/year can be produced with
a 2-strand continuous caster.
The sequence of the casting operation starts with inserting the
dummy bar into the mold to seal the bottom end. Molten steel
is then poured into the mold from the tundish while taking great
care to prevent contact with the air. The withdrawal of the
cast strand is started by pulling the dummy bar downward. The
molten steel flowing into the mold is rapidly cooled and forms
a thin solidified shell composed of fine granular crystals on
the surface and an array of fine columnar dendrites inside.
The solidified shell becomes thicker due to the growth of columnar
dendrites as it descends through the mold. A lime silicate flux
is added to the molten steel surface in the mold to prevent heat
loss from the molten steel surface and absorb nonmetallic inclusions
as they surface. This flux also infiltrates between the mold
and the cast strand, and provides lubrication which also prevents
sticking of the cast strand to the mold during the oscillation
of the mold. At the same time, the layer of mold flux between
the steel and mold reduces heat transfer and avoids a rapid decrease
in the temperature and resulting deformation and crack formation
of the strand.
Surface defects are formed on the cast strand when the level
of the steel bath fluctuates in the mold. The level is therefore
measured with a sensor and kept as constant as possible by controlling
the flow rate of molten steel from the tundish. Electromagnetic
braking of the melt flow in the mold is now a representative
technique for meniscus level control. The cast strand, which
still contains unsolidified molten steel, exits the mold and
is withdrawn downward while being supported by a group of rolls
and water-cooled with the sprays. During this process, columnar
dendrites continue to grow, and equiaxed dendrites are finally
formed to complete solidification. At this time, the solidified
shell is subjected to high thermal strain, shrinkage, and transformation
caused by cooling, and to ferrostatic pressure. Since the hot
solidified shell is substantially lower in strength and toughness,
the cast strand is susceptible to surface and internal cracks.
Consequently, during spraying the cooling pattern is carefully
controlled to prevent the growth of cracks due to strain while
ensuring solidification by cooling. This pattern control involves
controlling the intensity of the water-mist spray along the widthwise
and drawing direction of the cast strand as required by the steel
grade. Reduction is then applied to the cast strand at the crater
bottom to reduce center segregation. After cutting to length
with gas torches, the cast piece, or slab, is delivered to the
hot-rolling process.
As the productivity of the cast strand has increased and defects
have decreased to the extent that no off-line surface conditioning
by scarfing and grinding is required, hot-charge rolling and
hot direct rolling have been widely adopted. In hot-charge rolling,
the hot slab is charged into the reheating furnace, but is rolled
without substantial reheating, while hot direct rolling is performed
immediately after casting, omitting the reheating process completely. |
|
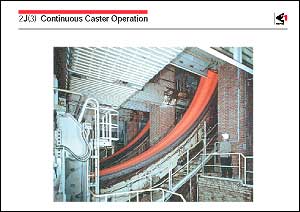 |
 |
 |
|
|