The exhaust gas emitted from automobiles
is one cause of air pollution, and various efforts have been
made to prevent this problem. One of the preventive measures
is the system shown in the figure. The exhaust gas from a gasoline
engine forms condensed water containing the ions of ammonia (NH4-),
sulfuric acid (SO42-), chlorine (Cl-), nitric acid (NO3-), carbonic
acid (CO32-), etc. when it is cooled. These ions are very corrosive
and create a very severe environment for materials. The whole
external surface of an exhaust system must also have corrosion
resistance to the deicing salts used in cold districts and to
atmospheric salt in coastal districts.
The components downstream from the muffler of an exhaust system
must have sufficient corrosion resistance to withstand the internal
attack of condensed water containing these corrosive ions and
external attack of these salts. The materials mainly used for
these components are low-carbon ferritic stainless steel incorporating
not less than 11% chromium. The components nearer to the engine
in front of the muffler need high oxidation resistance, because
they are heated to about 773K (500 ) during operation.
The exhaust manifold, which is heated to the highest temperature,
must possess both high-temperature strength and resistance to
thermal fatigue. High-chromium stainless steel is now used mainly
for these upstream components. As a result, the life of the exhaust
system has been substantially extended.
In addition to these efforts to improve corrosion resistance,
it is also necessary to gain economic improvements by reducing
the weight of the complete exhaust system. Material development
is being carried out at present to achieve this result. |
|
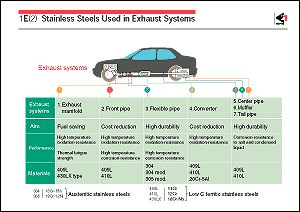 |
 |
 |
|
|