Electricity is transmitted from
power stations to the point of final consumption through electric
cables and transformers. During this transmission, power loss
occurs due to copper loss and iron loss. Copper loss occurs due
to the Joule effect. When an electric current flows overcoming
the electrical resistance of the conducting cable, some fraction
of electricity is converted into heat and lost. The amount of
copper loss is estimated to be about 5% of the total power demand.
Iron loss refers to the power loss caused by the iron core material
in a transformer, and the amount of this iron loss is estimated
at about 1% of the total power demand.
Motors and transformers are also used in the final stage of converting
electrical energy. Here again, copper loss and iron loss are
incurred in the material used for these devices. The power loss
attributable to iron losses at this stage is estimated to be
2.4% of total power demand. In consequence, the total iron loss
amounts to 3.4% of the total power demand. The annual power demand
is 850 billion kWh in Japan and 11,750 billion kWh in the world
(statistics from THE INSTITUTE OF ENERGY ECONOMICS, JAPAN, 1990).
Therefore, the annual power loss due to iron losses is equivalent
to approximately 29 billion kWh in Japan and approximately 400
billion kWh in the world. The amount of power lost in the whole
of Japan is equivalent to 1.5 times the annual power generated
by Kashima 4.4GW Thermal Power Station, the largest power station
in Japan. Power loss caused by iron losses can be reduced by
improving electrical steel sheets.
The figure shows the past year's record regarding the iron loss
value of electrical steel sheets for transformers, taking the
highest-grade products as an example. The iron loss value varies
depending on the saturation magnetization and frequency of alternative
current, but the values shown in the figure are those obtained
at a saturation magnetization of 1.5 tesla and a frequency of
50 Hz. In the period from 1940 to 1960, iron losses were greatly
decreased through the development of grain-oriented electrical
steel sheets with controlled crystal orientation which made it
possible to secure silicon contents as high as 3.25% with no
significant decrease in saturation magnetization. Subsequently,
iron loss continued to decrease, thanks to the practical application
of technology for reduced impurity element concentration in steel,
improved insulating films, reduced steel sheet thickness, and
other improvements. Iron losses were decreased further through
higher integration of crystal orientation in the 1970s and the
practical application of technology for refining the magnetic
domains to decrease hysteresis loss in the 1980s.
Such a decrease in the iron losses of electrical steel sheets
has also greatly contributed to down-sizing and to the efficiency
of motors for home appliances, including refrigerators, washing
machines, and air conditioners, and has resulted in decreased
power loss during the transmission of electric power. It is expected
that a further decrease in the iron losses of electrical steel
sheets will contribute greatly to achieving "sustainable
development", and will thereby improve human life while
saving energy resources and producing less environmental pollution. |
|
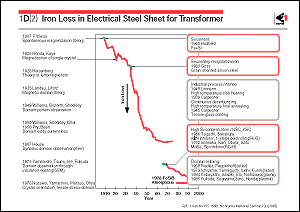 |
 |
 |
|
|