Flat products which must provide
corrosion resistance are coated after annealing. Typical hot-dip
coated products include galvanized strips for automobiles, building
materials and home electrical appliances, and tin- and chrome-plated
strips for food and beverage cans and other containers. For
reasons of efficiency, coating of continuous strip is more common
than coating of cut sheets.
Coating processes are broadly divided into hot dipping and electroplating.
The hot dip process is more suitable for heavy coating weights,
and electroplating for lighter coatings. Electroplating is often
used to apply a thin coat of expensive tin, and hot dip is used
for heavy coatings of inexpensive zinc. The figure shows an
example of a hot dip galvanizing line.
After passing through the pretreatment tanks for degreasing,
pickling, and cleansing, the strip passes through the annealing
furnace and a pot containing molten zinc. The annealing furnace
is used to apply the heat cycle needed to obtain the required
mechanical properties and activate the surface with a reducing
gas, which makes it easy to coat zinc on the strip surface.
The coating weight is controlled by a purge gas jet blown on
both surfaces of the strip from a nozzle above the pot, to remove
excessive molten zinc.
The cross section of a galvanized strip is composed of the steel
substrate, iron-zinc alloy layers, and a zinc layer. Because
the paint adhesion and weldability of the surface of this zinc
layer are not necessarily good, galvannealing has been developed
to improve these properties. In the basic process for galvannealed
strip, the zinc-coated strip emerges from the pot and is heated
in a galvannealing furnace, forming an iron-zinc alloy layer
by the interdiffusion of iron and zinc coating layer, so that
the surface of the zinc layer also contains some amount of iron.
The galvannealing line is usually equipped with a skinpass mill,
a tension leveler, and chemical treatment equipment for chromating,
following the galvannealing furnace.
For automotive steel strips, a thin iron plating is sometimes
applied electrolytically to the iron-containing zinc layer to
improve the sliding property between the die and material during
press forming and adhesion of paints in electrostatic coating.
In this case, electrolytic plating equipment is installed in
the line.
Typical products from a hot dipping line are galvanized sheets
and zinc-aluminum plated sheets for building materials, galvanized
sheets and galvannealed sheets for automobiles. Special products
are aluminum coated sheets for car mufflers and lead-tin alloy-coated
sheets (terne plates) for fuel tanks. |
|
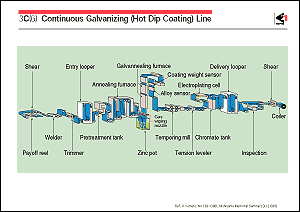 |
 |
 |
|
|