Steel material hardens after cold
rolling due to the dislocation tangling generated by plastic
deformation. Annealing is therefore carried out to soften the
material. The annealing process comprises heating, holding of
the material at an elevated temperature (soaking), and cooling
of the material. Heating facilitates the movement of iron atoms,
resulting in the disappearance of tangled dislocations and the
formation and growth of new grains of various sizes, which depend
on the heating and soaking conditions. These phenomena make hardened
steel crystals recover and recrystallize to be softened.
Furthermore, precipitates decompose to solute atoms which subsequently
dissolve into the steel matrix on heating and holding, then reprecipitate
in various sizes and distributions, depending on the rate of
cooling. These changes in the size and distribution of the grains
and precipitates also affect the hardness of the material.
The annealing of cold rolled coils has conventionally been conducted
by grouping and annealing the coils in batches stacked in a bell-type
furnace. This process is called batch annealing. However, continuous
annealing is now more commonly used. This type of annealing involves
uncoiling, and welding strips together, passing the welded strips
continuously through a heating furnace, and then dividing and
recoiling the strips. The figure shows a continuous annealing
line, which is composed of the entry-side equipment, furnace
section, and delivery-side equipment.
The main entry-side equipment comprises payoff reels, a welder,
an electrolytic cleaning tank, and an entry looper.
The furnace section comprises a heating zone, soaking zone, and
cooling zone. The cooling zone is divided into three sub-zones
so that complex cooling patterns such as cooling-heating-holding-cooling
can be performed. The delivery equipment comprises a delivery
looper, shears, and coilers, and may be linked to a temper rolling
mill and plating equipment as part of a larger continuous line.
The heating cycle applied to strips by continuous annealing differs
from product to product, but the three patterns shown in the
figure are typical. For cold-rolled strips for general use, it
is normal practice to adopt a heating pattern in which the strip
is heated to 973K (700 ) for about 1 minute, rapidly
cooled, held at about 673K (400 ) for 1 to 3
minutes to precipitate the solute carbon, and then cooled to
room temperature.
Although the total equipment length is 150 to 300m, the total
length of the strip in the line is as much as 2,000m. The travel
speed of the strip is 200 to 700 m/min. However, a recently developed
line for can material passes strip 0.15mm in thickness at a maximum
speed of 1,000 m/min. To operate such lines, speed control, tension
control, and tracking control of the strip are necessary, in
addition to a high level of automatic temperature and atmosphere
control. |
|
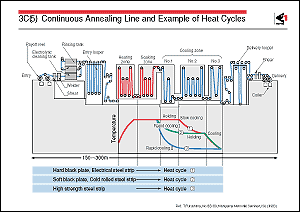 |
 |
 |
|
|