Strip thickness h2
on the delivery side of the rolls is equal to the work-roll gap
under load if the elastic deformation of the material is excluded.
As given by Eq. 1, h2 is the sum of
S0 and S, S0
being the work roll gap without load and S the amount
of deformation of the rolling mill under load. The S is given by
rolling force P divided by mill modulus M, so the delivery side
strip thickness is dependent upon the rolling force. The S, which is of the order of millimeters, cannot be
neglected when calculating the delivery side strip thickness.
Equation 1 is shown by curve (a) in the figure, which is called
the elastic deformation curve of the mill.
Rolling force P, which can also be determined by deformation
theory, is expressed in Eq. 2 as a function of material factors
and rolling conditions. Mean deformation resistance km is a function
of the rolling reduction, rolling speed, rolling temperature,
and material chemistry. In terms of geometrical relationships,
the contact arc length L is related to both the roll radius and
rolling reduction, as shown in Eq. 3. Equations 2 and 3 indicate
that the rolling force increases as the mean deformation resistance
of the material, entry side strip thickness, and amount of rolling
reduction increase. This relationship is represented by curve
(b) in the figure. This curve is called the plastic deformation
curve of the material in rolling. The delivery side strip thickness
is determined by solving Eqs. 1, 2, and 3, and corresponds to
the point of intersection of the two curves in the figure.
During rolling, the rolling force and the delivery side strip
thickness change if some variation occurs in the roll gap, the
mean deformation resistance caused by a variation in speed and
temperature, or the entry side strip thickness. In other words,
a change in the delivery side strip thickness can be instantaneously
detected by monitoring the rolling force. When the rolling force
changes, the delivery strip thickness can always be kept constant
by adjusting So in Eq. 1 by the amount required to compensate
for the rolling force difference. This is the principle of automatic
gauge control (AGC). |
|
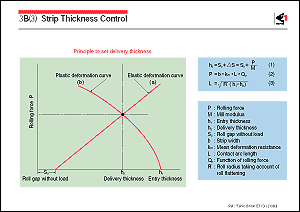 |
 |
 |
|
|