The figure shows an example of
the material balance of a top-and-bottom blown BOF. The low scrap
ratio operation normally practiced in Japan consists of the following
sequence. A small amount of scrap is charged in advance of the
pretreated low-silicon hot metal as the main raw material, and
the melt is refined by blowing pure oxygen gas. To produce 1
ton of molten steel, 1,033 kg of hot metal, 28 kg of scrap, 11kg
of ferroalloys, 23 kg of burnt lime, and 50 Nm3
of pure oxygen gas are required. In the area where higher scrap
operation is more economical, the scrap ratio can be increased
up to about 15wt %. After blowing for 20 minutes, the carbon
concentration is decreased from about 4% to 0.05%, and the temperature
rises from 1,473K (1,200 ) to 1,903K (1,630 ). The purpose of blowing in the BOF is to decarburize
and attain a sufficiently high tapping temperature. Hence, blowing
is finished when the carbon concentration and temperature of
the molten steel have reached these target values. On tapping,
alloys and deoxidizers such as silicomanganese and/or aluminum
are added to the molten steel in ladle. In the subsequent secondary
refining process, the molten steel is degassed and alloys are
added to make the final adjustments needed to reach target compositions.
The operation of the BOF starts with tilting of the vessel. Scrap
and then hot metal are charged into the vessel, the vessel is
returned to the upright position, and the multi-hole lance for
top-blowing pure oxygen is inserted from the throat and lowered
to near the surface of the hot metal. Blowing starts with a supersonic
jet of pure oxygen gas impinging on the metal bath and, at the
same time, an inert gas is blown from the furnace bottom to stir
the bath. In the initial stage of blowing, the silicon in the
hot metal is oxidized to form silica which reacts with the burnt
lime and iron oxide additions and forms a CaO-SiO2-FeO
slag. At the same time, the temperature in the furnace rises
and the scrap starts to melt. The carbon concentration of the
hot metal is high in the initial stage of blowing, so the pure
oxygen gas reacts efficiently with the carbon to form carbon
monoxide and decarburization proceeds. At this stage, decarburization
is controlled by the pure oxygen feed rate, and the bath temperature
rises progressively as decarburization proceeds. With the progress
of decarburization and the consequent decrease in carbon concentration,
the decarburization reaction is controlled by the rate of carbon
transfer in the molten steel to the oxygen gas/molten steel interface.
If the transfer of carbon by the stirring of the molten steel
is insufficient, the pure oxygen gas is consumed to oxidize iron
rather than reacting with carbon. This results in an increase
of iron oxide in the slag and a decrease in the yield of iron.
To prevent this, gas blowing from the furnace bottom is increased.
Oxygen blowing from the main lance was controlled in the past
by using a static blowing model, which incorporates the composition
and temperature of the charged materials, thermodynamic quantities
of reactions involved, the degree of wear of the furnace refractories,
the combustion ratio of the exhaust gas, and other factors. The
model was based on the material balance, heat balance, and calculated
thermodynamic factors and reaction rates. In the static blowing
model, the quantity of pure oxygen gas to be blown in is determined
by computing these balances and fine tuned by inputting heat
data to the model each time blowing is carried out. It is more
common now to use, on top of the static control, dynamic control
in which the carbon concentration and temperature are measured
by the sublance near the end of the blowing. The amount of pure
oxygen gas to be injected is then adjusted using measured values,
and blowing comes to an end when the target value has been attained.
The essential points of BOF operation include:
(i) How to raise the rate of hitting the target values of carbon
concentration and temperature at the end of blowing with only
one blowing operation.
(ii) How to raise the oxygen efficiency for decarburization,
the yield ratio, and production performance.
(iii) How to reduce wear of the furnace refractories, the consumption
of auxiliary raw materials and pure oxygen gas, and heat loss.
After the end of blowing, the vessel is tilted and the molten
steel is poured from the taphole into a ladle. At this time,
ferroalloys, and deoxidizing and desulfurizing agents are added
to the molten steel in the ladle. In the final stage of tapping,
various kinds of slag stoppers are used to prevent the BOF slag
from flowing into the ladle, since the slag has a strong oxidizing
power and reoxidizes the molten steel. |
|
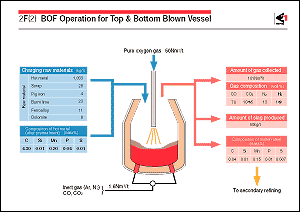 |
 |
 |
|
|