Steel materials are required to
have their own characteristics according to the application and
operating conditions. The metallographic factors governing these
characteristics are now better understood and manufacturing technology
for controlling these factors has advanced, making it possible
to improve these characteristics. One good example is that of
bearing steels.
Bearings are used to support the axis of rotation in machinery
and equipment, including automobiles. The structure of a bearing
comprises an inner ring and an outer ring, between which steel
balls or rollers are sandwiched. Friction is thus minimized by
converting a sliding action into a rolling action.
The figure shows the relationship between bearing life and the
oxygen content of steel. The bearing life under a given load
is expressed as the total number of revolutions until fatigue
flaking occurs on the surfaces of the inner and outer rings or
steel balls due to the repeated loading. Failure is generally
a probability phenomenon, and bearing test samples show large
variation in life tests, depending on the surface roughness of
the rings and balls and on the lubrication conditions. For this
reason, tests are conducted on many bearing samples under given
conditions, and the number of revolutions equivalent to a 10%
probability of failure is regarded as the life of the bearing.
When the oxygen content of steel is decreased from 10 ppm to
5 ppm (i.e., when the nonmetallic oxide inclusions are decreased
by about half), bearing life is much improved, as shown in the
figure. Life varies with the same low oxygen content of about
5 ppm due to differences in the size and composition of the oxides.
Hard aluminum oxides and large oxides of over 30μm are especially
harmful. The life of bearing steels is greatly dependent on the
cleanliness regarding the amount of nonmetallic inclusions. For
this purpose, the secondary refining process described later
is used to achieve the required ultra-high level of cleanliness,
the refining operation being conducted to remove the nonmetallic
inclusions and minimize reoxidation of the molten steel. In consequence,
at present a value of 3 to 6 ppm is obtained industrially in
steels of the lowest oxygen content. By reducing the amount of
large inclusions and lowering the oxygen content, bearing life
has been extended by almost 30 times in comparison with steels
having an oxygen content of about 20 ppm. |
|
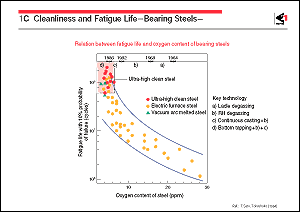 |
 |
 |
|
|