The raw materials for iron and
steel will become increasingly diverse and of lower grade in
the future. Recycling scrap of various grades of iron resources
will increase in the future, and the use of direct-reduced iron
will also increase. The direct use of coals as reducing agents
will increase, and measures to implement degrading coals will
be enhanced to provide more effective utilization of less expensive
resources. Flexible processes capable of accommodating fluctuating
product demands will be necessary.
Quality requirements for steel products have become increasingly
stringent, requiring a manufacturing process that can ensure
a precise composition control, composition uniformity, and very
low levels of impurities. These requirements will be met by
better refining and solidification processes.
The purpose of a manufacturing process is to manufacture the
required amount of products of consistent quality as efficiently
and economically as possible and to deliver these products on
time. This requires extended equipment life and increased productivity
of facilities by synchronization, continuation, and integration
of elementary processes using improved automation and advanced
control technology. In elementary processes, where automation
and control have already been realized, processing of material
from an upstream process is possible with minimal disturbances,
constant quality, and delivery to the next process on time.
These elementary processes compose the whole system, and, as
a result of integrating these elementary processes into the whole
system, material flows in the proper quantities throughout the
process. Furthermore, the occurrence of defective products is
minimized in intermediate processes. Products of the required
quality can be manufactured in the necessary amounts when required,
without excess. If the conventional elementary process can
be simplified or omitted in the course of system integration,
the benefits become even greater. This is exemplified by the
omission of both the ingot making and primary rolling processes
and their replacement by continuous casting, and by the simplification
of annealing by the continuous process. Other examples include
the continuous rolling of slabs. This has been accomplished
by rolling slabs in the roughing mill into sheet bars, in-line
welding of the resulting sheet bars, and continuously rolling
the welded sheet bars in the hot strip mill without interrupting
the rolling operation. Also included is the replacement of continuous
slab casting and hot rolling of specific steel grades by strip
casting, which will become a commercial process very shortly
for austenitic stainless steels.
In processes which are now under development, more emphasis will
be placed on environmental protection and energy saving. Attempts
to solve these problems have already started, and some examples
are described in the following sections. |
|
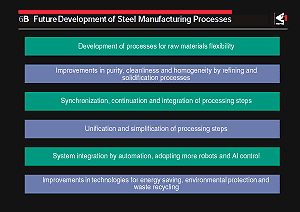 |
 |
 |
|
|