The production of iron and steel
necessarily requires the use of the carbon in coal to reduce
iron ore. As long as coal remains indispensable as the reducing
agent, the greatest measure available to the steel industries
to cope with global warming is to reduce the consumption of energy,
including that of coal.
The smelting and refining processes, involving coke ovens, the
BF, and the BOFs, generate heat and pressure, which are recoverable
as steam and electric power. Representative examples of practical
recovery techniques include dry quenching at coke ovens and the
top-pressure recovery at blast furnaces. The former involves
quenching coke with nitrogen gas instead of water, enabling the
sensible heat of the high-temperature coke to be efficiently
recovered and utilized for the boilers. The latter example generates
electric power by driving a turbine with the pressure of the
exhaust gas from the top of the BF. The sensible heat of the
exhaust gas produced in the BOF is also effectively recovered
by an exhaust gas boiler. Moreover, the exhaust gas is used
at the rolling processes as fuel gas for the reheating furnace
and the annealing furnace.
One of the most effective ways to save energy involves the omission
or continuation of specific operating processes. Examples are
(i) the change from ingot making - slabbing to continuous casting,
thereby reducing the fuel required for soaking the ingot and
power for driving the slabbing mill, (ii) adoption of hot charge
rolling or hot direct rolling of continuously cast slabs, thereby
reducing fuel consumption for reheating, and (iii) changing from
batch annealing to continuous annealing. These changes have enabled
steel works to reduce their energy consumption considerably.
The recovery and effective utilization of energy, as well as
the omission or continuation of operating processes, will remain
important issues for the steel industry of the future.
In the countries where plentiful steel scrap is available, scrap
based steelmaking with EAF, preferably coal based new melting
furnaces in the future, contributes considerably to energy saving
since the scrap route (waste recycling) does not require the
energy intensive iron ore reduction process which calls for about
70 percent of total energy needed to produce steel via iron ore
route with BF and BOF. This issue will be discussed later in
Sections 6F and 6G.
Furthermore, improving the quality and properties of steel products
contributes greatly to energy saving. For instance, high strength
steel sheets for automotive applications reduce fuel consumption
by making it possible to decrease the weight of the car body.
Steel materials widely used in machinery and equipment which
are to generate or consume electricity also make an important
contribution to energy saving. For example, gas turbines operate
more efficiently at higher applied gas temperatures. The heat
resistance of the steel materials used for the turbine blades
and rotor shafts determines this gas temperature. The development
of higher heat-resistant super alloys and stainless steels is
therefore closely associated with increased generating efficiency.
It has already been mentioned that a lower iron loss in electrical
steel sheet increases power conversion efficiency. Improved
corrosion resistance in weatherproof and surface-treated steels,
as well as longer life in bearing steels, contribute greatly
to energy saving by extending the life cycle of equipment fabricated
from these materials. |
|
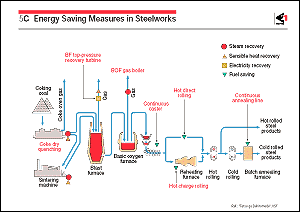 |
 |
 |
|
|