Working methods include rolling,
forging, extrusion, and drawing. The most basic of these is rolling.
When a wide strip is rolled between two rolls, it is possible
to neglect the deformation in the width direction and treat it
merely as two-dimensional deformation in the thickness and length
directions, except at the edges of the strip. Vertical stress
P and horizontal stress Q are generated in the material between
the rolls. P is a stress caused by the compressive load from
the rolls, while Q is a stress generated when the deformation
in the rolling direction is restrained by the portions of the
strip before and after the strip in contact with the roll. Frictional
force Pr is generated by the friction between
the material surface and the roll surface. On the entry side,
this frictional force acts in the direction of delivery, because
the circumferential speed of the roll is higher than the material
speed. On the delivery side, however, the frictional force acts
in the direction of entry, because the material speed is higher.
The point at which the two speeds become equal is called the
neutral point. Taking a micro volume which has unit length in
the width direction of the roll in the oblique-lined region of
Fig.(a), if stress P and stress Q are assumed to be constant
within the thickness, and the friction coefficient is assumed
to be constant over the whole arc of contact, Eq. 1 can be derived
by considering the force balance in the horizontal direction.
Equation 2 is a yield criterion which shows that, in order for
the material to develop plastic deformation, the shear stress
generated by stresses P and Q must reach the shear yield stress
of the material. P and Q can be calculated by solving Eqs. 1
and 2. The distribution of vertical stress P is shown in Fig.(b),
where stress P has its peak at the neutral point. The rolling
force per unit width is calculated by integrating stress P over
the whole arc of contact. Furthermore, the rolling torque can
be calculated by integrating the moment around the roll shaft
caused by stress P.
The rolling force is the most basic value used in the determination
of the deformation induced by a rolling mill and the resulting
strip thickness on the delivery side. It must be evaluated as
accurately as possible. When dealing theoretically with improvements
in the thickness accuracy and profile of a rolled strip, it is
necessary to reflect, in the rolling force, both the distribution
of stresses in the thickness direction and the deformation of
strip in the width direction. A finite element method which permits
three-dimensional analysis can be used for this purpose.
Heat is generated by the deformation of the material and the
friction between the material and the rolls, consequently, the
temperature of the rolls and of the material rises, and roll
wear also occurs. This results in the occasional sticking of
the rolls to the material. Water and/or rolling oil are supplied
to the contact area between the rolls and the material as a means
of lubrication to reduce the friction, and hence the rolling
force and rolling torque, thereby minimizing these problems.
Taking the above factors into account, several methods of determining
rolling force and its widthwise distribution have been developed.
The optimum choice will depend upon the local conditions under
consideration. |
|
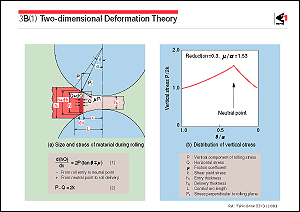 |
 |
 |
|
|