In the conventional process for
hot strip production, slabs about 250mm in thickness are reheated
in a furnace, and hot rolled one after another by a roughing
mill to 30 to 60mm in thickness, and then rolled by a finishing
mill to target thicknesses with a range of 0.8- 25.4mm.
In this process, the head and tail ends of each strip are finish-rolled
and both ends run out to the coiler without tension between the
coiler and finishing mill stands, and hence tend to pass unstably
on the roller table, for instance, jumping and/or weaving. This
tendency is larger with thinner thicknesses, and is one reason
that hot strip with a thickness of less than 0.8mm cannot be
produced by the conventional process.
The two ends of the strip are different from the middle in size,
profile, and properties because of the instability in the finish
rolling. The ends are generally cut off to produce a uniform
strip, but this results in a yield loss equal to the amount of
the discarded ends. Furthermore, the interruption of the rolling
operation caused by the rolling interval between slabs and slow
starting and finishing speeds of finish rolling to avoid unstable
rolling reduce productivity.
Yield and productivity can be improved by continuous rolling
of several slabs, which is termed "endless rolling".
Endless rolling was realized for the first time in the world
in the new Hot Strip Mill at Kawasaki Steel Corporation's Chiba
works in 1996. The layout of the plant is shown in the figure.
The main equipment of the plant comprises three reheating furnaces,
a sizing press, which reduces the slab width, three roughing
mills, a coil box, a joining device (sheet bar welder), a 7-stand
finishing mill, a strip shear, and two down coilers.
To conduct endless rolling, it is necessary to continuously supply
sheet bars to the finishing mill by joining the tail end of the
preceding sheet bar to the head end of the succeeding sheet bar
at the joining device. Joining must be finished before the tail
end of the preceding sheet bar is fed into the first stand of
the finishing mill. The permissible duration for joining is therefore
shorter than the finish rolling duration of one sheet bar, and
usually is about 20 seconds. Furthermore, the head end of the
succeeding sheet bar must arrive at the joining device at the
proper timing for joining. A coil box with three positions of
retained sheet bar coils is provided to perform the following
functions: Sheet bar rolled by the roughing mill is coiled at
the leftmost coiling position, held for adjustment of the joining
timing at the waiting position in the middle, and then is uncoiled
at the rightmost uncoiling position.
After finish rolling followed by cooling, the strip is divided
by the high speed strip shear installed before the down coilers.
In dividing and coiling strips, it is important to instantaneously
stop the tail end of the preceding strip and to guide the head
end of the succeeding strip running at a high speed to the next
coiler.
In endless rolling, joined sheet bars can be finish-rolled stably
at a constant speed over their whole length without interruption,
improving the uniformity of strip qualities such as dimension,
profile, and microstructure through the whole length. Yield is
also improved because crops are not cut. Yield and productivity
are estimated to increase by 0.5-1.0% and by 20%, respectively.
Furthermore, with this new process, hot strip with a thickness
of less than 0.8mm can be produced. |
|
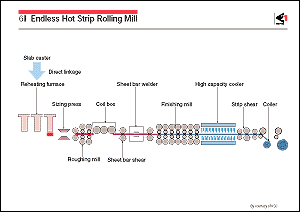 |
 |
 |
|
|