The steel scrap-EAF route of steelmaking
requires substantially lower primary energy consumption (70kg
in terms of carbon) and associated CO2
evolution than the Iron ore-BF-BOF route (440kg in terms of carbon)
to produce one metric ton of steel. This substantial difference
is attributed to the considerable energy required to reduce iron
ore into iron in the latter route.
For the time being, perhaps even in the very near future, no
technologically effective means will be made available to stabilize
evolved CO2 and prevent the CO2
accumulation in the atmosphere. Measures to be taken are, therefore,
the reduction of CO2 evolution (reduction
of fossil fuel consumption) for the sustainable development.
Recycling of steel scrap considerably contributes to this goal.
Accordingly, energy and environmental issues encourage the use
of the scrap-EAF route. So far, the scrap-EAF route has been
used mainly to produce either long products (shapes, bars, rods
and wires) of commodity grades in large quantity from obsolete
and prompt industrial scrap or the same and forgings of high
quality grades mostly from home-and/or prompt industrial scrap.
In recent years, however, the new thin slab casting technology
has enabled scrap-EAF steelmakers to produce flat products. Thin
slab casting technology was pioneered by SMS, Germany, in the
Compact Strip Process (CSP), and reached operational maturation
at Nucor Steel Inc., USA. Similar processes have subsequently
been developed, including the In-line Strip Process (ISP) of
Demag/Arvedi. Thin slabs are cast into either a funnel shaped
taper mold or straight taper mold 60-100mm in thickness at the
outlet, subject to reduction to about 50mm in thickness during
strand withdrawal while they still retain a liquid core, and
reduced in-line to about 30mm in thickness followed by hot rolling
with tandem hot strip mill consisting of a smaller number of
roll stands. An integrated line comprising an advanced EAF-thin
slab caster can produce up to about 1 million ton/year with much
lower investment in facilities and much less energy consumption.
The typical composition of such mills is shown schematically
in this figure. There has also been considerable progress in
improving the efficiency and productivity of EAFs, including
preheating of scrap, continuous feeding of scrap, twin shell
furnaces, and a variety of DC-Arc furnaces. Combined with such
EAFs, technology has made it possible to eliminate roughing mills
and to carry out in-line rolling at an attractive investment
wherever scrap is available. As the thickness of the slabs is
about 30-50% that of conventional continuously cast slabs, the
casting speed should be two to three times higher, or about 6m
per minute for a thin slab caster with 1 million ton /year of
production. In such high speed casting, some steels sensitive
to cracking tend to suffer surface degradation and in an extreme
case of medium carbon peritectic steels, casting cannot yet be
performed due to deterioration of slab surfaces by crack formation.
This difficulty should be overcome by further development of
the process. In view of the increasing generation of scrap in
the industrialized countries, the scrap-EAF-thin slab caster
combination will gain an increasing share in world steel production.
Qualitywise, these steelmakers have concentrated on the commodity
grades, but now are upgrading to high quality products, including
deep drawing steels. Obvious limitations for the upgrading are,
however, that the scrap-EAF route should not cause either deterioration
of the properties of the resulting steels due to residuals such
as Cu, Sn, As, Sb, Bi, or associated pollution from accompanying
volatile residuals such as Zn and Pb and waste such as some plastics,
which generate harmful dioxines. |
|
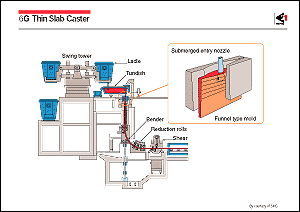 |
 |
 |
|
|