As shown in the figure, the continuous
caster is composed of a tundish, a mold, a mold oscillator, a
group of cast-strand supporting rolls, rolls for bending and
straightening the cast strand, rolls to pinch and withdraw the
cast strands, a group of spray nozzles, a torch cutter for cutting
the cast strand, a dummy bar for extracting the cast strand at
the start of casting, and other components.
The continuous billet caster casts round or square strands of
small cross-section, and the continuous bloom caster casts strands
of large cross-section. Both are used to produce materials for
wire rod, bars, shapes, and pipe. The continuous slab caster
produces wide rectangular strands of large cross-section, which
are cut off as slabs for use as material for sheet and plate.
Slabs for flat-rolled products are usually cast with a thickness
of 100 to 250mm. In recent years, however, continuous casters
which produce thinner slabs 30-80mm in thickness have been introduced.
The thin slab caster eliminates the need for a roughing mill
in the hot-rolling process. However, the steel throughput is
limited to 1 million ton/year per strand in this process by the
thin slab thickness even at higher casting speed, which is currently
limited to about 7m/min. Consequently, the thin slab caster is
usually combined with an electric furnace of matching output.
This combination has been favorably adopted by minimills.
The types of continuous casters include: (i) the vertical type,
in which the mold and support rolls are arranged vertically;
(ii) the vertical-and-bending type, in which the solid shell
of the cast strand is bent in the horizontal direction at the
position where solidification is sufficiently complete; (iii)
the curved type, in which a curved mold and support rolls are
arranged on an arc of the same radius, and the cast strand is
straightened horizontally at the end of solidification; (iv)
the vertical-and-progressive-bending type, in which the mold
and a group of upper support rolls are arranged vertically and
the cast strand still with a liquid core is progressively bent,
and then progressively straightened to the horizontal position
at the end of solidification; and (v) the horizontal type, in
which the mold and support rolls are arranged horizontally. The
vertical type is used to cast high-grade steels because it promotes
the separation (by flotation) of nonmetallic inclusions poured
into the mold, although the construction of the caster building
becomes tall and hence expensive. The curved type is mainly applied
for mass production of conventional products, because building
costs can be reduced by the lower height. The vertical-and-progressive-bending
type, which combines the advantages of the vertical and curved
types, is being used increasingly for large sized slab casters
which require improved quality and productivity. The horizontal
type is used to produce billets on a small scale because the
equipment and the building costs are comparatively low.
Refractory nozzles are used to transfer the molten steel from
the ladle to the tundish and then to the mold and prevent any
reoxidation through contact with air. To avoid the entrainment
of top slag, the bath depth of the tundish is increased, and
dams and weirs are installed in the tundish to promote the separation
of nonmetallic inclusions by flotation. The nozzle between the
tundish and the mold, called the submerged entry nozzle, is designed
in such a way that nonmetallic inclusions are not carried deep
into the strand together with the molten steel flow, and therefore
are not captured in the solidifying shell of the cast strand.
A device for controlling the molten steel flow exiting from the
nozzles by applying a magnetic field to the flow in the mold
is also used for the same purpose and for improving the surface
of the shell by suppressing turbulence of the melt meniscus.
The mold is equipped with an oscillator (60-240cpm, 4-10mm amplitude)
to prevent sticking of the cast strand to the mold. The support
rolls are of high rigidity and the roll interval is short to
minimize bulging due to ferrostatic pressure, preventing subsequent
cracking and segregation due to such bulging. Water or water-mist
spray nozzles for cooling are provided across the full width
of the cast strand, from immediately below the mold to the crater
bottom. Electromagnetic stirrers are sometimes installed below
the mold and between the support rolls to stir the molten steel
in the solidifying shell by electromagnetic induction and thus
to increase the equiaxed dendrites, and to disperse the segregation
of solute elements at the crater bottom position between many
equiaxed dendrites. A device for applying a thicknesswise reduction
to the cast strand is often provided at the crater bottom position
to squeeze the solute enriched molten steel to the upper unsolidified
molten steel. These two devices are often used in combination
because neither by itself is fully adequate for preventing the
segregation of solute elements. |
|
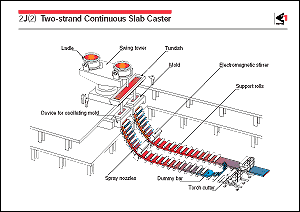 |
 |
 |
|
|