Heating in an electric furnace
is made by electric energy. Raw ferrous materials consist mostly
of scrap, some cold pig iron and DRI. For this reason, the electric
furnace plays an important role in the recovery and recycling
of waste iron resources. In areas where an abundant supply of
scrap and electric power are available, the proportion of steelmaking
via the electric furnace route is relatively high, because both
energy consumption and equipment investment are substantially
smaller than via the integrated route using a BF and BOF to produce
steel from ore. Electric furnaces are classified as arc furnaces
or induction furnaces, according to the heating method. The
arc furnace is used far more extensively for steelmaking because
its capacity is large and production efficiency is high.
In addition to melting, both oxidation refining and reduction
refining are possible in the arc furnace; the former is used
for decarburization, dephosphorization, and dehydrogenation,
and the latter for desulfurization and deoxidation. The arc
furnace is also capable of melting a higher fraction of alloy
scraps. For this reason, it is often used to refine high-alloy
steels, such as stainless steel. However, with the introduction
of secondary refining processes such as the argon oxygen decarburization
(denoted AOD hereinafter) and vacuum oxygen decarburization (VOD)
processes, which are exclusively used for refining stainless
steel, the role of the arc furnace has been limited to high-efficiency
melting in the upstream process. Even with commercial grades
of carbon steel, it is common to conduct high-efficiency melting
and decarburization in the arc furnace and to finish the process
with a separate secondary refining furnace.
The efficiency of heating, melting, and decarburization in the
arc furnace has been substantially increased by adopting an ultra
high-power transformer and oxy-fuel burner, as well as by injecting
coal powder and pure oxygen gas. Cooling and protecting the
furnace walls and ceiling with water-cooled panels has also been
enhanced, enabling an increase in production efficiency from
80 to 120 ton/h. Recent trends have seen a shift from the alternating-current
arc furnace to the direct-current arc furnace, the introduction
of preheating and continuous charging equipment for scrap, and
the adoption of the eccentric furnace-bottom tapping. The DC
arc furnace offers lower unit consumption of power, electrodes,
and refractories, and both noise and flicker are also lower.
The preheating and continuous charging equipment for scrap decreases
the energy consumption because preheating is carried out by the
high-temperature exhaust gas, and heat loss by opening the furnace
lid during conventional scrap charging can be prevented. The
eccentric bottom-tapping allows efficient tapping without tilting
the vessel, and is desirable for maintaining the cleanliness
of the molten steel, because the carry over of oxidizing slag
into the ladle during tapping can be prevented. |
|
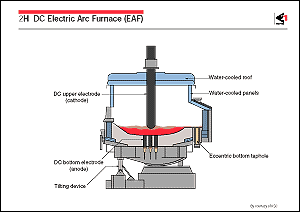 |
 |
 |
|
|