The figure shows a flowchart of
the integrated manufacturing process for iron and steel using
the blast furnace and basic oxygen furnace (denoted BF and BOF
hereinafter, respectively), which is presently the most commonly
used method (51% of world steel production). After the BF-BOF
process, molten steel is controlled to a target composition and
temperature and is then cast by continuous casting machine to
produce slabs, blooms, and billets. These castings are rolled
to the required dimensions by the rolling mill to produce steel
products. The smelting and refining process for iron and steel
in the BF-BOF process involves the carbon reduction of iron ore
(Fe2O3) in the BF to make molten iron, and decarburization of
molten iron in the BOF to make molten steel.
Major reducing agent in the BF is the carbon monoxide gas(CO)
generated by the oxidation of the carbon(C) in coke. Consequently,
carburization takes place at the same time as reduction, producing
hot metal(molten iron) containing about 4% carbon. The hot metal
is decarburized to the required carbon content in the BOF. The
main reaction in this process is the oxidization of the carbon
in the hot metal by both pure oxygen gas (O2) and iron oxide
(Fe2O3). The residual oxygen, after contributing to this decarburization
reaction, remains in the molten steel. This oxygen is fixed
and removed by deoxidation reagents such as silicon and aluminum
as SiO2 and Al2O3 or is removed as carbon monoxide gas in the
subsequent vacuum degassing process.
In addition to the BF-BOF process, there is another process which
utilizes mainly scrap as an iron source, with some direct reduced
iron whenever necessary. The direct reduced iron is produced
by reducing iron ore with reformed natural gas, whose principal
components are hydrogen, carbon monoxide, and methane. The scrap,
along with direct reduced iron, is then melted in an electric
arc furnace (denoted EAF hereinafter) to produce molten steel
which is subsequently processed by the continuous casting machine,
as mentioned above.
The molten steel from the BOF and EAF is then deoxidized and
alloying elements are added in the prescribed amounts. The molten
steel is then held at the target temperature and continuously
cast, and the castings obtained are cut to the prescribed length.
After heating to the rolling temperature in a reheating furnace,
these castings are hot-worked to the required products. Steel
shapes, bars, and wire rods are worked on section and bar mills
and wire-rod mills equipped with caliber rolls, plates are worked
on reversing mills, and hot-rolled steel sheets are worked on
hot strip mills. After pickling to remove scale from the surface,
the hot-rolled steel sheets are worked to cold-rolled steel sheets
on reversing mills or tandem rolling mills, and the cold-rolled
steel sheets are tinned or galvanized as required to produce
various surface-treated steel sheet products. Steel pipe is
produced by forming and welding steel sheets or plates, or by
piercing a billet and rolling to the final dimensions without
a seam. |
|
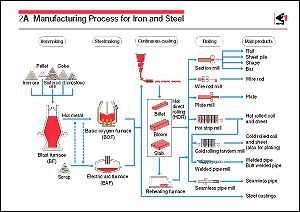 |
 |
 |
|
|